AIㆍ드론ㆍVR…생산 효율화부터 작업자 안전까지 책임지는 기술
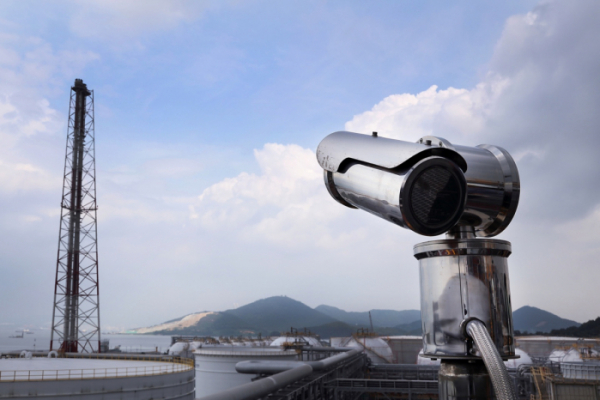
12일 찾은 GS칼텍스 여수공장의 1공장 내 방호상황실에선 공장 내·외부 상황을 한눈에 볼 수 있는 폐쇄회로(CC)TV 화면이 실시간으로 송출된다. 이곳에서 관리하는 250여 개의 CCTV 중 약 164개는 인공지능(AI) CCTV다. AI 분석 기술을 통해 화재나 외부 침입 등을 감지한다.
송출 화면에는 노란색 또는 분홍색의 사각형 그래픽이 합성돼 있다. 노란색은 화재나 불꽃, 분홍색은 침입을 인지하는 구역이란 뜻이다. 만약 제한구역에 침입자가 나타나면 화면 위에 알림이 뜨고, “침입 감지”라는 음성 메시지가 상황실 내에 울린다. AI CCTV의 감지 측정률은 99%에 달한다.
GS칼텍스는 전사 차원의 디지털 전환(DX) 작업을 추진하고 있다. 장치산업 특성상 설비 관리 역량이 곧 기업 경쟁력으로 직결되는 만큼 디지털 기술을 활용해 생산성과 수익성을 높이겠다는 전략이다.
특히 80만 개 이상의 설비들이 유기적으로 연결된 여수공장을 중심으로 전방위적 DX를 추진해 현재까지 100여 건 이상의 과제를 수행하고 있다.
강재민 GS칼텍스 디지털혁신팀장은 "DX 활동에서 가장 중요한 건 현장의 취약점을 찾고, 이를 디지털 기술로 어떻게 해결하는지"라며 "공정운전 최적화, 설비 통합 관리, 탄소 배출 저감, 안전 환경 보건, 생산 계획 최적화 등의 분야에서 DX를 추진하고 있다"고 설명했다.
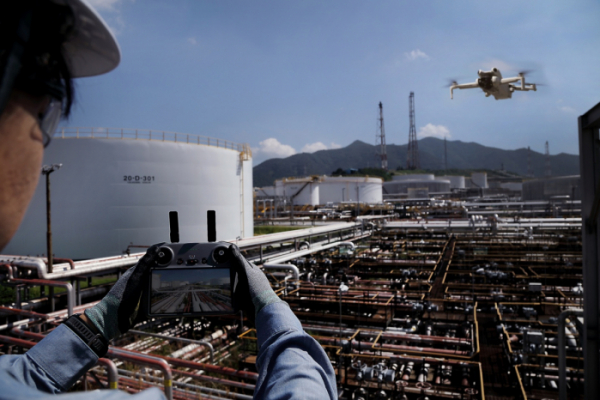
설비 통합관리 영역에서는 데이터 분석에 기반한 설비관리 통합 플랫폼을 도입해 프로세스를 최적화하고 있다. 이를 통해 공장 가동률 개선과 비용 절감 효과가 기대된다.
주요 회전기계에 생긴 문제를 조기에 감지하고, 발생 원인을 분석하는 AI 기반 시스템도 마련했다. 배관 두께를 측정할 때도 엑스레이(X-Ray) 촬영 이미지 분석에 AI를 활용해 정확도를 높였다.
생산·설비 부서에서는 드론을 적극적으로 활용한다. 외부검사 드론은 넓은 면적을 효율적으로 관리하고, 접근이 어려운 지역까지 접근할 수 있다. 내부검사 드론은 어떤 환경에서도 안정적으로 비행하고, 다양한 검사 장비를 탑재해 위험 지역의 설비도 안전하게 점검할 수 있다.
공장운전 및 생산 최적화 분야에서는 플래닝 데이터 플랫폼(PDP)을 구축해 원유·제품 가격 전망, 시장 예측 등의 모든 데이터를 바탕으로 효율적인 의사결정을 내린다.
또한 머신러닝 기술을 활용해 코크(원유 정제 시 나오는 고체 부산물) 발생 함량을 예측하고, 선제적으로 대응할 시간을 확보할 수 있게 해준다. 가열로의 연소 효율을 정밀하게 모니터링하고 관리할 수 있는 시스템도 구축했다.
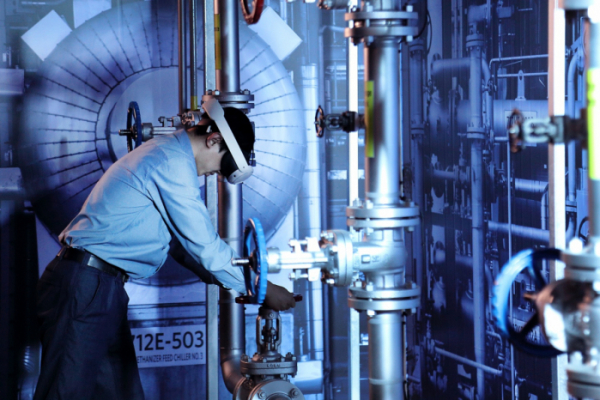
작업자 안전을 위해서도 디지털 기술이 사용된다. 가상현실(VR)·증강현실(AR) 기반의 안전 교육 프로그램을 마련해 작업자들이 위험 상황을 가상으로 체험할 수 있도록 했다.
GS칼텍스는 임직원들의 디지털 역량 내재화를 위해 지난해부터 ‘디지털 아카데미’를 운영해 내부 전문가를 육성하고 있다. 또 전 직원이 참여할 수 있는 ‘DX 데이’를 개최한다.
GS칼텍스는 지속가능한 DX로 성공 사례를 쌓아 정유·석유화학 업계에서 벤치마킹하는 기업이 될 수 있도록 세계경제포럼(WEF)이 선정하는 ‘등대 공장’ 인증을 추진할 방침이다. 등대 공장은 4차 산업혁명의 핵심 기술을 도입해 제조업 혁신을 이끄는 공장을 가리킨다.
김성민 GS칼텍스 생산본부장(각자대표 부사장)은 "최근 2조7000억 원을 투자해 에틸렌을 생산하는 MFC(Mixed Feed Cracker)를 가동하며 차별화된 제품과 서비스를 국내외에 공급하고 있다"며 "기존 사업의 안정적 성장과 함께 딥 트랜스포메이션(대전환)으로 100년 기업으로의 도약을 준비하겠다"고 말했다.